Welcome to Sprocket School! This project is maintained by volunteer editors. Learn more about how this works. |
Kinoton FP 30 E: Difference between revisions
No edit summary |
mNo edit summary |
||
Line 111: | Line 111: | ||
==External links== | ==External links== | ||
* [http://my.kinoton.com/fileadmin/user_upload/film_equipment/manuals/E_series/FP30E-PREMIERE_e.pdf Kinoton FP30E Premiere manual] | * [http://my.kinoton.com/fileadmin/user_upload/film_equipment/manuals/E_series/FP30E-PREMIERE_e.pdf Kinoton FP30E Premiere operating manual] | ||
Revision as of 14:04, 21 April 2020

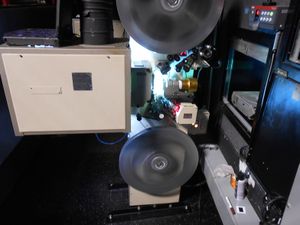
The Kinoton FP 30 E is a 35mm projector that features a unique electronically-controlled direct-drive intermittent. It provides excellent image stability and offers a number of features designed to reduce print wear. For this reason, FP 30 Es are a common choice for archives, museums, studios, and other high-end screening rooms. The models most commonly used for theatrical exhibition are the FP 30 E and the FP 30 E PREMIERE, although some high-end screening rooms employ the FP 30 E-S.
The FP 30 E shares many parts and features with the dual-format FP 38 E and FP 75 E.
History
The first projector in the E series was the FP 30 EC, released in 1989 for studio and lab use. The more basic FP 30 E was released for standard theatrical exhibition in 1997, and was updated to incorporate the improved PREMIERE intermittent in 2007.
During the industry-wide transition to digital projection Kinoton ceased production of their film projection equipment, and the company was liquidated in 2014. The Kinoton brand survives under a new company, Kinoton Digital Solutions. Although the new company inherited the unsold inventory from the film projector manufacturing operation, parts are difficult to acquire. The company also intentionally destroyed their manufacturing equipment, so the designs cannot be easily reproduced by a third party. This, in addition to the use of consumable plastic parts and a design that relies on complicated electronic systems, means that the Kinoton E series will likely have a shorter support life than traditional mechanical projectors.
Variations include:
- FP 30 E - The base model designed for theatrical exhibition.
- FP 30 E PREMIERE- The later base model featuring an updated intermittent unit with a faster pulldown, increasing light output by 25%.
- FP 30 E-R - A model for theatrical exhibition with the ability to shuttle film in reverse for “rock-and-roll” operation.
- FP 30 E-S - A basic studio model also used for exhibition, providing greater control over transport speed, the ability to project in reverse, and a magnetically controlled sound drum that moves out of the film path when the film is not up to speed in order to prevent impedance scratches.
- FP 30 E-Q - A higher-end studio model primarily used for post-production, with the ability to interface with external devices in order to synchronize playback for mixing, and even greater speed control that includes the ability to pause playback and project a still frame.
- FP 30 EC - The top-of-the-line studio model, with even greater speed range and control, more precise tension and gate pressure control, and the ability to advance or rewind following a time code. The EC was released in 1989 as the first projector in the E series, and was replaced with the improved EC II in 1999. Later models feature the improved REFERENCE intermittent.
Intermittent
E series Kinotons have an electronically controlled intermittent instead of the typical Geneva drive. The intermittent sprocket is controlled by a stepper motor that is synchronized with the main drive that controls the continuous sprockets. An encoder on the main drive counts the frames being advanced by the upper continuous sprocket, and a microprocessor times the pulldown of the intermittent.
As a result of this unique design, the function of the intermittent varies from traditional mechanical intermittents in a number of ways.
- The sprocket begins rotating continuously during the motor ramp-up, then switches to intermittent motion once the motor is up to speed.
- The framing is reset to its default position when the projector is power cycled. The first time the motor ramps up after the projector has been powered on, the intermittent resynchronizes with the main drive, which resets any adjustments made to the framing. The framing position will remain consistent thereafter until the projector is turned off.
- The framing is continuous. Whereas framing is set on mechanical projectors by adjusting the position of the intermittent sprocket within a fixed range of motion (ex., Centuries use a rack and pinion), the framing on an E series Kinoton can be shifted in either direction indefinitely.
- Because the framing is electronically controlled, it can be performed remotely.
Framing position
The framing position resyncs every time the projector is power cycled, and the default position may be significantly out of frame. It is therefore advisable to set the framing position by running test film before the first screening of the day.
Do NOT turn the projector off between running the test film and the public screening. The framing position will be reset.
Electronically-Controlled Friction Drives
Kinoton’s electronically-controlled friction drives are designed to reduce print wear by automatically calibrating film tension. The drives have sensors that can estimate the amount of film on the reel, allowing the frictions to adjust the force applied over the course of playback. This is an improvement over traditional friction clutches, which can only be set to a fixed tension despite the fact that the optimal tension will shift as the roll diameter changes during playback.
The friction drives are engineered to apply the correct tension to a wide range of roll sizes, ranging from reels that hold over 6,000’ of film down to split reels with 2” cores.
While the electronically-controlled frictions were a popular option, the base model of the FP 30 E came with mechanical frictions that used traditional friction clutches.
Friction Controls
The frictions are controlled by toggle switches on the lamphouse side of the pedestal. There are toggles for setting the size and friction direction for the feed and takeup reels as well as an on/off toggle.
The small reel setting should be use for reels between 1,000’ and 3,000’. The large reel setting should be used for any reel above 3,000’.
Note that the direction of the arrows on the toggle switch indicates the direction of the friction required to keep tension on the film, NOT the direction that the reel will be spinning. The friction direction on the feed reel will be the OPPOSITE of the direction of the reel’s rotation, since it applies holdback tension. On the takeup reel, the direction of the friction will be the same as the direction of the reel rotation because the friction drives the takeup.
Lenze Frequency Inverter
The drive system is controlled by a Lenze frequency inverter. By modulating the frequency of the current running to the main drive motor, this unit can control the RPM of the motor and therefore the film transport speed.
Parameters that may be modified from the factory default to achieve a desired functionality include:
- Motor ramp-up time - This should be timed for changeover projection, and a pair of changeover projectors should be configured to share the same ramp-up speed.
- Playback speed - There are two parameters for playback speed, which are set by the factory to 24fps and 25fps (the latter accommodates the 50hz utility frequency used in some regions). However, either can be modified according to the demands of the venue. For example, in American venues the 25fps slot can be reprogrammed to accomodate a lower frame rate for silent film. The basic FP 30 E has a range of between 10 and 30fps.
- POS speed - The speed at which the POS button advances the film.
Variable speed
Some FP 30 Es have a variable speed option. For these projectors, the speed is controlled by a rotary switch that ranges from 10-30fps, and the speed is displayed on a digital read-out. Instead of the 24/25fps toggle button on the control panel, there is a button that toggles between 24fps and variable speed.
FP 30 Es that were not originally manufactured for variable speed can be reconfigured to accommodate a specific frame rate by adjusting the Lenze inverter parameters for one of the two default speeds. In the United States, this can be accomplished by overwriting the output frequency for 25fps, replacing it with one that will drive the motor at the correct RPM to achieve the desired frame rate. Likewise, in regions with a 50Hz utility frequency, the 24fps setting can be overwritten. After this change is made, the projectionist can toggle between 24fps and the custom frame rate using the 24/25fps toggle. The relationship between output frequency and frame rate can be determined by running the projector at the default settings and checking the readout on the inverter to determine the hertz at a given frame rate (ex., if the output frequency is 16Hz at 24fps, the frequency in Hz should be ⅔ the desired frame rate).
The Lenze inverter should only be adjusted by a qualified technician, so any change to the frame rate should be coordinated well in advance of the show that requires an alternative frame rate.
When reconfiguring the projector to run silent film at a lower frame rate, the cooling plate behind the aperture will also likely need to be replaced. The default cooling plate for non-variable speed FP 30 Es covers the soundtrack area, while those manufactured for variable speed operation have a wider opening to illuminate the full silent aperture. A 1.33 aperture plate and a properly sized lens with the correct horizontal offset for the silent frame are also required.
Film Break Sensors
The FP 30 E is equipped with two infrared film break sensors. The first is located between the first pair of guide rollers beneath the feed reel, and the second is located between the lower continuous sprocket and the last guide roller. These sensors must detect film in order for the projectors to operate. If they fail to detect film during playback, the projector will stop and the dowser will close. In addition to stopping the projection in response to a film break, these sensors will stop the projector if the feed reel begins to race, and the projector cannot start if the the film is not threaded over the sensors with adequate tension.
These sensors also stop the projector at the end of every reel. As the tail leaves the feed reel it loses tension over the upper sensor, causing the motor to stop and the changeover dowser to close. This can cause the projector to shut down prematurely if the tail is too short. If the distance between the last frame of picture and the end of the tail is shorter than the distance between the aperture and the feed reel, additional leader must be spliced to the tail.
When running test loops, the sensors can be bypassed by covering them with artist tape.
Skate Pressure
The skate pressure is maintained by an omega spring attached to the skate block. A knob on the front of the projector adjusts the spring compression, which in turn governs the amount of pressure the spring applies to hold the skate against the film.
A pressure gauge is located below the skate. The skate pressure is not calibrated, so the gauge only provides a nominal value. The omega spring can also be bent by hand to allow the mechanism to achieve a higher pressure than the factory default.
This design applies less pressure to the film than the other common projectors such as Centuries or Simplexes, but as with any projector the minimum amount of pressure should be used in order to reduce wear to the print, the intermittent, and in the case of the Kinotons, the plastic skate and runners.
To achieve the proper skate pressure, back it off by rotating the control knob clockwise until the picture becomes slightly unsteady, and then increase pressure by turning it counterclockwise until the image is stable. You will also hear increased chatter from the lower loop when the pressure is too low.
Cleaning
Most cleaning can be accomplished with a soft, lint-free cloth and a toothbrush. Persistent dirt can be removed with 99.9% alcohol.
In the gate, dirt tends to accumulate on the runners and on the ceramic discs that serve as lateral guides. The runners and discs should be checked between every reel and cleaned accordingly. If the discs are dirty, they should be removed and wiped clean. Before replacing them, clean the recess using a cloth and brush. After reinserting the disc, spin it to make sure it rotates freely and brush off any additional dirt that is picked up by the disc as it makes contact with the deeper areas of the recess. This recess will also accumulate dirt over time, and must be cleaned periodically. There is a concave cavity between the disc and the runners which can be cleaned by removing the disc and inserting an alcohol-soaked cotton swab.
The inboard O-ring on the pinch roller tends to accumulate a lot of dirt. This should be checked and wiped clean between every reel. To do so, pull the roller away from the sound drum in order to let it spin freely. After cleaning the pinch roller, it can be rotated in order to drive the sound drum. Slowly turn the pinch roller and examine the surface of the sound drum for dust or residue and clean accordingly.
With the projector OFF, periodically clean the interior of the shutter housing. If you attempt to remove the housing with the projector on, you will damage the shutter blade.
When the spindles become dirty, they should be cleaned using 99.9% alcohol. After cleaning, apply a drop or two of oil to the spindle shaft.
Consumable Parts
Skate
When the plastic is chamfering where it meets the ceramic discs, the skate is too worn and should be replaced. A new skate will have to be filed down in order to fit perfectly.
Gate runners
Run your fingernail laterally across the runner. If you can’t feel the inside groove, flip the runner 180 degrees. When both sides are worn, replace.
Ceramic rollers
When the discs start to wear, flip them. When both sides are worn, replace.
Pinch roller O-rings
Replace if cracked.
Key lamps
When replacing key lamps, be warned that the gels will jump out when removing the plastic cover. Once the cover has been removed, the lamp can be removed with needle nose pliers, but be gentle to avoid breaking the glass. Insert the new lamp and replace the cover.
Framing light
Turn the projector OFF before removing the shutter housing to avoid damage to the shutter blade. After removing the shutter housing, use a fuse puller or hook something behind the light to remove it.